
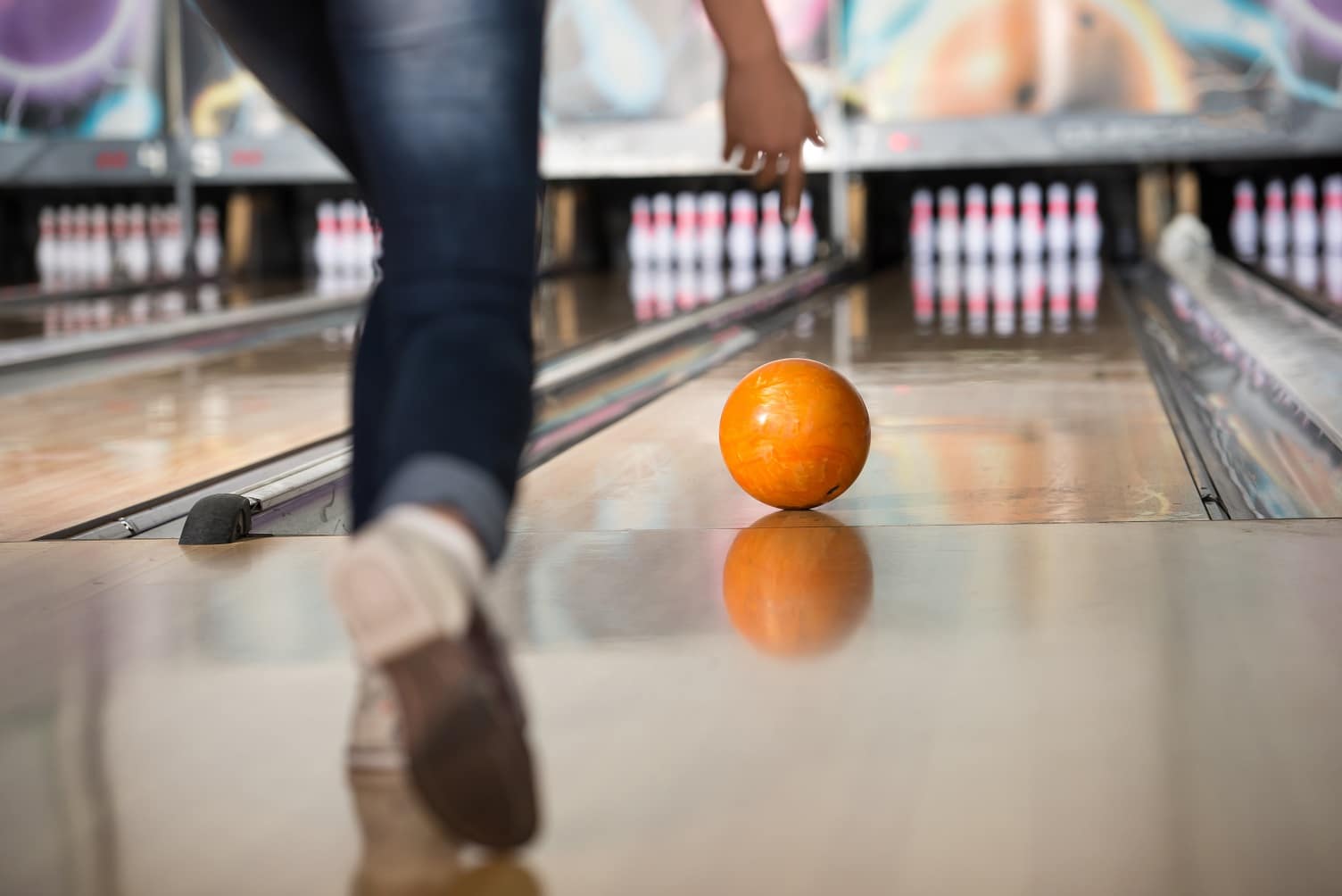
"Pin down" layouts place the pin between the finger holes and the thumb hole, while "pin up" layouts place the pin further from thumb hole than the finger holes (see photos). Layout is determined with reference to each bowler's positive axis point (PAP the pocket end of the ball's initial axis of rotation). Layout and grip See the section titled, Effect of coverstock, core and layout on ball motionĪ ball's drilling layout refers to how and where holes are drilled, in relation to the ball's locator pin and mass bias (MB) marker. Hook potential has increased so much that dry lane conditions or certain spare shots sometimes cause bowlers to use plastic or urethane balls, to purposely avoid the larger hook provided by reactive technology. Within the reactive category are solid reactive coverstocks (having the greatest amount of microscopic pores), pearl reactive coverstocks (including mica additives that enhance reaction on dry lane surfaces), hybrid reactive coverstocks (combining the mid-lane reaction of solid coverstocks and the back-end reaction of pearl coverstocks), and particle coverstocks (including microscopic silica particles, favored for use on heavy oil volumes). Ball manufacturers developed closely guarded proprietary blends including ground-up material such as glass, ceramic or rubber, to enhance friction. In the "particle-enhanced" balls developed in the late 1990s, microscopic particles embedded in reactive coverstocks reach through oil lane coatings to provide even greater traction. The early 1990s brought development of reactive resin ("reactive") balls by introducing additives in urethane surface materials to create microscopic oil-absorbing pores that increase the "tackiness" that enhances traction. Urethane balls developed more friction with the newly developed polyurethane lane finishes of the day, sparking the evolution of coverstock technology to pursue ever-stronger hooks with correspondingly higher entry angles. Polyester ("plastic") balls were introduced in 1959 and, despite developing less hook-generating lane friction than rubber balls, by the 1970s plastic dominated over rubber balls which then became obsolete with the early-1980s development of polyurethane ("urethane") balls. Ĭoverstock technology See the section titled, Effect of coverstock, core and layout on ball motion A rough timeline of ten-pin bowling ball coverstock technology īowling balls were made of lignum vitae (hardwood) until the 1905 introduction of rubber balls. These figures are up from one ounce (28 grams) following the Augrule change. The USBC permits three ounces (85 grams) of static side weight and three ounces (85 grams) of top weight. The USBC banned weight holes (balance holes) in competition, effective August 1, 2020, to prevent their changing ball dynamics. USBC specifications include physical requirements for weight (≤16 pounds (7.3 kg)), diameter (8.500 inches (21.59 cm)-8.595 inches (21.83 cm)), surface hardness, surface roughness, hole drilling limitations (example: a single balance hole including the thumb hole for "two-handed" bowlers ), balance, plug limitations, and exterior markings (structural and commercial), as well as requirements for dynamic performance characteristics such as radius of gyration (RG 2.46-2.80), RG differential (≤0.06), and coefficient of friction (≤0.32). The USBC and World Bowling promulgate bowling ball specifications. Reactive resin coverstocks increase hook potential. A reactive resin ball with a pin up layout (note green dot), the mass bias indicator visible.
